Explore the world of Concorde with Heritage Concorde
Heritage Concorde - Project Salute
Report on how the Heritage Concorde engineers have been working to improve the display of
Concorde G-AXDN at Duxford, by making the nose move.

The project started late in 2012 when we attended our first core members’ meeting at Duxford; in attendance were Graham Cahill, Steve De Sausmarez (Founder), Ian Mosdell, John Dunlevy and Gaute Lund. We spent about 5 hours walking around the aircraft, discussing how Heritage Concorde could look to the future and at the same time Steve handed operations over to Graham.G-AXDN is owned by Duxford Aviation Society (DAS) and is part of their British Airliner Collection.While we were in the cabin of the aircraft, a DAS Volunteer overheard our discussions and asked for some history of our group; of course Ian, Steve and John were only too happy to talk about both Heritage Concorde and G-AXDN. The chairman of DAS, David Garside was also on the aircraft, and we were lucky enough to be introduced and allowed to visit the cockpit.

The conversation quickly turned to how the museum wished to improve the visitor experience and they asked if we had any suggestions. We said we would put our heads together and make some suggestions.A number of ideas were generated including that of making G-AXDN the only Concorde outside Le Bourget to have an animated nose.
Possible options were discussed and we began to make our enquiries.We quickly secured the support of a major hydraulics supplier in the UK, Hydraulics Online Ltd, who agreed to help with the technical design work and supply some of the required equipment free of charge. It was separately agreed that Ian Mosdell would be the lead engineer responsible for the project.
On 21st March, 2013 the core members of Heritage Concorde returned to the museum for an inspection of the aircraft wiring for our project “Return to Light”. We met with David Garside and presented our proposal. Attending the meeting were Graham Cahill, Ian Mosdell, John Dunlevy and Gaute Lund.While John Dunlevy was completing his checks for the Return to Light project Ian Mosdell and Chris Giles went below to inspect the hydraulic systems for the aircraft’s nose.
Ian was surprised to find the systems in good condition, thus increasing the chances of successfully completing the project. The nose on G-AXDN had been lowered and raised in the 1980’s but we were keen to enable the DAS to do it whenever they wanted to and with little effort - this would increase the fundraising potential for the DAS significantly.

Images
Left G-AXDN
Right G-AXDN nose down in the 1980's (Unknown copyright)

Preliminary inspection: Ian Mosdell inspects the hydraulic systems on board G-AXDN

Chief engineer Ian Mosdell inspects the hydraulics on G-AXDN for the first time

Chief engineer Ian Mosdell inspects the hydraulics on G-AXDN for the first time

Chief engineer Ian Mosdell inspects the hydraulics on G-AXDN for the first time

Chief engineer Ian Mosdell inspects the hydraulics on G-AXDN for the first time

The visor jack is inspected along with the rest of the system for problems we may encounter

Although some surface rust was found the system was in remarkable condition

Nose Jacks are inspected and we are satisfied to continue

The visor jack is inspected along with the rest of the system for problems we may encounter
Further progress on the project was delayed when a number of potential “show-stopping” issues were raised; a full Health & Safety risk assessment and method of work statement were needed before the project could continue. We worked together with Duxford Aviation Society volunteers and staff to address these requirements successfully.
The Heritage Concorde team provided a 28volt power supply to power the nose electrics and the specialist hydraulic power pack that was designed, built and donated by Hydraulics Online Ltd was ready by mid-June.
Graham Cahill visited Hydraulics Online Ltd on 20th June, 2013. After a tour of the premises, Mark Tonks (Managing Director) presented the hydraulic power pack to Graham.I have to say it has been a real pleasure dealing with Mark, Helen and the team at Hydraulics Online Ltd; they have been very accommodating throughout, giving expert advice backed up by full written technical specifications and, of course, have provided the equipment to the museum all free of charge.

Hydraulics Online Ltd present the power pack to Graham Cahill for use on the project

Hydraulics Online Ltd present the power pack to Graham Cahill for use on the project. Left Mark Tonks, Right Graham Cahill

Closeup of the power pack

Hydraulics Online Ltd present the power pack to Graham Cahill for use on the project
Visit Hydraulics Online Ltd by clicking the link above.
If it’s hydraulic we can design it, supply it, solve it or repair it... So let us take the pressure!
Next we needed oil Gaute Lund (Seen Left below) sourced and paid for the oil from the USA. We have since been donated all remaining stock of original M2V oil from ExxonMobil, we would like to thank them for this most generous donation.





(Day two of work) 30th July 2013
In attendance : Graham Cahill, John Dunlevy, Philip Cairns
Account of the day written by Graham Cahill.
The plan was for John to continue with the Return to Light project with Philip fully inspecting the existing hydraulics.The day started well when we were told by DAS that all the paperwork and Health &Safety requirements were in place and they asked when we could proceed with the project.
Philip started the inspection of the hydraulics system by removing each panel in the droop nose section and thoroughly inspecting all aspects of the mechanism including the: track rails, actuators, swivel joints and flexible pipes.
He found the system to be in good order, but did however add some recommendations to our already growing list of “things to do” to protect the aircraft.Here are a few photos from the inspection:

Some of the parts you don't usually see

Some of the parts you don't usually see

Some of the parts you don't usually see

Some of the parts you don't usually see

Phil Cairns works with DAS engineer Chris Giles on the inspection

Inspection panels removed

Phil Cairns stops to smile for the camera while inspecting

Phil Cairns works with DAS engineer Chris Giles on the inspection
I hadn’t met Philip before. He is a really skilled engineer, an all-round nice guy and it was a real pleasure to see him and John working together on the aircraft. I felt very lucky to join them and I am looking forward to seeing the whole team together soon. Philip’s made a number of recommendations including the investigation of an unconnected hydraulic pipe in the nose section and full inspection of the landing gear pins.
The Plan.
G-AXDN was outside for nearly 20 years and despite being in really good internal condition, all precautions had to be taken to protect the aircraft from damage and to protect the public from injury.
The engineers had by now collectively compiled a plan detailing of all the work and tasks that needed to be undertaken up to and including the movement of the nose. The engineers plan and health and safety assessment are published as separate documents to avoid confusion with this report.
We briefed the volunteers and staff at DAS and they were more than happy for us to progress… sooner than later! It was strange; we had been waiting for the final go ahead and now it was all systems go to get the job done but always with safety in mind.
(Day three of work) 13th August 2013
In attendance : Graham Cahill, John Dunlevy, Ian Mosdell
Ian Mosdell made a further inspection of the aircraft, paying particular attention to the issues previously raised by Phillip Cairns.The unconnected hydraulic pipe turned out to be just a random pipe that had been left in the nose section – it was not even a Concorde part! The landing gear pins were inspected and were in place and ok.
In addition Ian cleaned and greased the visor rails.
All electrical connectors were removed, cleaned and sprayed with very good contact cleaner. Micro-switches were exercised where possible.
All the internal panels in front of the nose actuators had been removed before, possibly when the nose was raised in the 1980’s but all the hoses and pipes are present and do not have solid oil in them. In fact the entire nose hydraulic system was found to be in excellent condition with no solidified hydraulic oil or crystals.

The connection used in the 1980's was found

Return pipe to Right Supply to left

A close up of the connection made in the 1980'd to lower and raise the nose

The connection used in the 1980's was found
The next stage
We needed appropriate connectors and hydraulic lines to connect to the pump and then to Concorde we intended to remove the pipes fitted in the 1980’s and connect direct to the aircraft this was to reduce the amount of connectors and joints in the system. We also wanted quick disconnects on the pump end so DAS could remove the hoses easily and quickly if required. These were ordered and arrived quickly

Ian poses for a photo

John and Ian discuss how to proceed

Ian poses for a photo
(Day Four and five of work) 1st & 2nd October 2013
In attendance : Graham Cahill, John Dunlevy, Ian Mosdell
We visited Duxford to complete the preperation work.
Ian completed the work schedule very quickly and installed the Hydraulic lines which were donated by the Heritage Concorde team.
We ran the lines through the cabin vent inlets to avoid damage to the aircraft.
John meanwhile was preparing the electrical systems for the nose to operate, he cleaned the wiring systems
We install a sounder to the aircraft (Pictured below right) which is one of the stipulations for H&S we had to comply with. The plan is to sound the sounder before and after nose movement.

The lines exit the aircraft in a non destructive way

The connections are made with as little joints as possible

Oil lines exit through and existing vent which can be replaced in the future

The lines exit the aircraft in a non destructive way

Ian has now completed all the preparation work required and is ready to put the oil into the power pack, this is significant as we are about to put oil into a UK Concorde for only the second time since 2003. (the first being Project Flagship)


Both Ian and John are now happy that we can apply fluid to the aircrafts systems, the next step is to flush and bleed the system, John needs to apply power to the nose system.
To ensure we fully comply with the H&S of the project we finish work for this visit, we need to make sure all the paperwork is in place because the next step is to add fluid to the aircraft which we can not do safely while the hanger is open.
In the meantime we need to produce a “safe working instruction sheet” for DAS to use when operating the nose this will include all instructions for the safe operation of the nose system.
The safe working document is published separately to avoid confusion with this report.
(Day Six of work) 22nd November 2013
In attendance : Graham Cahill, John Dunlevy, Ian Mosdell, Phillip Cairns, Tony Morrish
We met with DAS at 10am and they were happy to proceed, we finalised the insurance paperwork and went to the aircraft to complete other jobs as we could not work on the aircraft during opening hours.
It soon came round to 3pm and the whole team met for a H&S brief. the meeting ended and we started to prepare a workspace for commencement of the job.
At 4pm the hanger was closed and the engineers got to work, we waited for the airport fire brigade to attend (A stipulation of the IWM designed to protect the aircraft and hanger in the event of a fire)


The Breakers are closed and the nose systems come to life

The Breakers are closed and the nose systems come to life

The nose systems are alive and without hydraulic pressure we try them out, we hear the solenoids clicking as expected.

The Breakers are closed and the nose systems come to life
John inspected the wiring again and pressed the breakers to close, slowly the nose electrics were coming to life, one by one the breakers were pressed to close.
Once complete we could hear the solenoids clicking in the nose section exactly as expected.
The nose electrical systems are checked and once satisfied the fire brigade can leave, we have fire safety equipment available and to hand but we find the system is safe. Many thanks to Duxford Airfield fire service for taking time out to attend while the airfield is closed.
Ian and Philip were bleeding the system through at very low pressure to ensure no air was in the system.
Once the engineers all agreed that the system was bled through and we had no leaks at low pressure, we increased the pressure slowly up to 3500 psi. The engineers ran the system for some time to ensure no leaks occurred then inspected the entire nose system visually. We had absolutely no problems with leaks, everything went to plan.

Phil Cairns checks for leaks

The engineers check the system and bleed it through while DAS engineers look on.

Phil Cairns checks for leaks
The next step was to try to lower and raise the visor only, with John in the cockpit and Ian, Phil and Tony on the hanger floor watching the Visor down position was selected.
The visor glided down fully and perfectly.



The next step was to raise the visor, John selected the up position in the cockpit and the visor failed to raise.
The engineers spent a few hours inspecting the system and find that a solenoid valve has failed to operate.
We agree with the museum that it has been a productive day and that we will need to re visit in the coming weeks to investigate further and fix the problem.
DAS are keen to progress with the project and Heritage Concorde want to complete the job to the successful end.
The engineers pack up for the night and leave the aircraft with the visor down.
The day after 23rd November 2013
In attendance : Graham Cahill
Graham revisits the aircraft in the morning to take further pictures, check for oil and do some further work on one of our other projects. Here are some photo's taken on that day.





(Day Seven of work) 03rd December 2013
In attendance : Graham Cahill, John Dunlevy, Ian Mosdell, Tony Morrish
We revisit DAS to continue with the work,
The plan for the day is to investigate further the visor up circuit to find the fault.
We test the solenoid without hydraulic power using an external power supply to the correct pins and find it is operating correctly, we test the supply to the solenoid and find no 28 volt supply when the up selection is made. The possibilities are that the fault exists in the windscreen park system or the relays. Because this is a pre production aircraft the relays are in the cabin of the aircraft not under the floor, the maintenance manuals are all for production aircraft so we need the detail for this aircraft we spend some hours in the archives at Duxford to try to find the correct paperwork but it is not available.
We bypass the windscreen park system using the override in the cockpit and test again, we still have no power to the solenoid.
The tests and investigations have taken most of the day to complete and we still need to raise the visor back to its correct position.
The engineers check the wipers are correctly parked so we do not damage them when we raise the visor.
We then apply 28volts direct to the solenoid to signal the visor to raise and we apply low hydraulic pressure to the system. The visor raises as expected. The visor is left in an up and locked position ready for our next visit.

Left -
Visor up
Right -
Test Rig used to raise Visor

We are happy with the progress for the day and leave the aircraft.
(Day Eight of work) 28th January 2014
In attendance : Graham Cahill, John Dunlevy, Ian Mosdell, Tony Morrish, Gaute Lund
We are pleased to return to the aircraft after a Christmas break
The plan for the day is to continue with our investigation into the visor system on the aircraft.
We are pleased because DAS have bought a new power supply for the aircraft, the specification is 28v 32Amp protected power supply similar to the ones used for our return to light project.
This will be a far better option for the aircraft and enable us to do more things in the future.
John Dunlevy removes the old power supply and fits the new one in its place.
The power supply is tested and certified (PAT test) By the DAS electrician.
We have a short meeting with DAS to discuss how we plan to proceed and they agree they are happy for the work to continue.
We set up the inspection tower and prepare the aircraft for a visor lower, the hydraulics are applied and the aircraft powered and we lower the visor again. (The visor must be lowered to start the testing)
We temporarily remove some instruments from the cockpit to enable easy testing of the visor systems.
John Dunlevy starts with the fault finding on the aircraft and finds the fault just after lunch.


Photos: Left: John Dunlevy tests the systems Visor and nose down (5deg) Right: Phil Cairns gets a photo opportunity
John Dunlevy’s account of the fault find to the visor system.
The diagrams below should help with the explanation of how the fault was found.
Photos: Left: John Dunlevy’s fault finding diagram Right: Equipment positions on AXDN
28Volts was not found on pin D of the solenoid (far right on the LHS diagram) and the original defect.
We found 28Volts at pin A (supply to Visor/Nose selector switch) and B which is the output from the switch to the visor Uplock relay.
However we could not find 28Volts at pin D on the Nose Uplock Micro Switch (M24) either.
Between these two items are the Wiper relays (M30) and (M31) and the wiper over ride switch.
Only when both wipers are correctly parked (dedicated parking motors) and both relays operating can the visor be normally raised.
In an emergency however the override switch can be operated.
The override switch circuit is drawn to show how 28Volts can be bypassed around these two relays if the wipers are not completely parked.
We could not detect any voltage at the wiper override switch.
We did manage to power both emergency parking motors on both wipers and the RH wiper moved through a parking cycle.
We then moved the Visor/Nose selector switch from down to up.
It was during this process we could hear Relays faintly clicking in one of the bulkhead boxes we were trying to identify.
On removing the cover for inspection Relay M18 was found not to be firmly in contact with it's connector.
The associated electrical connector (supply to relay) was also removed/cleaned and refitted. We now had 28 Volts at pin D of the selector valve solenoid.
Interesting fault to fix.
John Dunlevy


We cycle the visor through several moves to ensure the system is working properly and Ian Mosdell checks the visor tracks are fully lubricated.
The hanger is now due to close to the public so we ask DAS for permission to progress with a nose move and they agree. We wait for the hanger to close and ensure no public are in the building.
We select visor down and the visor lowers correctly, we then select nose 5 degrees and the nose lowers as if the aircraft were still in operation.
Ian celebrates as the nose has lowered perfectly.We attempt to raise the nose using the aircrafts own systems and it takes 11 min to return and lock up, we have a further fault. We suspect only one of the 5 degree solenoids is operating correctly. We find that we can manually assist the nose to the zero degree position so we do this several times to clear air from the system.
It is late now and we decide to pack up, it has been a very productive day and G-AXDN’s visor works completely and as expected now. Our next visit will involve finding the fault with the 5 degree jacks. We return the aircraft to the nose up, visor up position and go home.

The video to the left shows the work for the day, once the visor fault was found we progressed to a nose move as explained above.
We will not be able to visit AXDN for some time due to the School holidays and our visit to Filton however we continue to discuss options to solve the issue
John Dunlevy has forgotton his radio again so discussions are had face to face.
Remedial work (away from the aircraft)
We investigate further and discuss how to proceed, we suspect that the nose solenoids have dried oil in them but to remove the solenoids means we have to remove the actuators which is a big job which will take a minimum of 12 hours to complete. We work on a fault finding list while away from the aircraft, we will complete it on our next visit. We work on a way of removing the solenoid units without removing the actuators. Below you can see a diagram of the actuators (Left) and a diagram of the whole hydraulic system (Right)


(Day Nine of work) 03 April 2014
In attendance : Graham Cahill, John Dunlevy, Ian Mosdell
The plan for the day is to run through some tests and try to remove one of the solenoids if the tests fail to produce results.We suspect that the solenoids are full of solidified oil and will need removal, cleaning and refitting but before we do this we investigate the standby system valve is out of the equation by bypassing it. The standby system valve was always a problem with Concorde and if not reset correctly it could cause the nose not to raise. As DAS are unlikely to require the standby system to ever operate the nose the standby valve is bypassed. A photograph of the standby selector valve is below.

We try the nose again and it fails to raise.
We run through some further checks including capping off each individual 5 degree jack and the nose still fails to raise.
We really do not want to remove the actuators so we work on a plan to do the job in situ.
Ian has come up with an ingenious plan to remove one of the 5 degree solenoids, we make the tools to complete the job on site. We are fast running out of time so we raise the nose and visor to remove the LHS 5deg solenoid unit.

Above; Actuators in position
Removal of the unit takes around 2 hours due to the tight access and we are now running late so we pack up and leave for the day.
We are now convinced that the solenoid valves are the problem but we will know more when we inspect the one removed from the aircraft. If they are blocked we will have to remove the remaining three, inspect and clean them and re fit on our next visit.


Left: Solenoid in position
Right A photo of the LHS Solenoid valve we removed
Remedial work (away from the aircraft)
The solenoid valve is completely stripped down while we are away from the aircraft.


Above : Picture of the Solenoid valve
Above : Picture of the Solenoid valve

Above : Picture of the Solenoid valve and parts from within

Above : We make the tools to service the valves next time we visit
Good news we find the valve is completely bunged up with solidified hydraulic oil, enough to stop the valve from working correctly

Above : Picture of the Solenoid valve and the solidified oil

Above : Picture of the solidified oil
The valve is cleaned fully and fitted back together, the o ring seals seem in good condition and are nice and tight on refitting.
We Decide that because of the state of the valve we have removed that the next few visits are about removal of each valve and refitting. We do this over the course of several visits, removing one valve and refitting a serviced one.
Below you can see some photo's of the various valves all being cleaned and serviced.
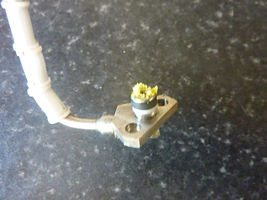
Above : Pipes clogged with M2V

Above : Tiny parts compared to a sewing pin

Above : Pipes clogged with M2V

Above : Part of a valve and the intricate components

Above : Solenoid valve completely clogged up
We find during the service of the valves that one of the magnetic pins in a solenoid has become detached, we ask Brooklands if they have any spare. They supply us with an entire actuator which we remove the part from, we fit the part.

Above : Solenoid loaned by Brooklands
Once all the valves have been serviced and refitted we try the nose again, we still have the fault.
We decide to bite the bullet and remove the actuators from the aircraft, this is a big job to do, we start the job on one visit then return to completely remove them on a second visit.

Above : Both Actuators assembled
We also remove the Hydraulic power pack because Hydraulics Online Ltd have recommended an upgrade which will increase the pressure and reduce air and dirt in the system.
We completely strip the actuators down to their basic parts but we do not break into the actuator itself, this is a specialist job which we can not complete. We find some of the pipes are blocked with Crystallised M2V so we clear them.



Above : Collet lock switches
Above : Actuator being reassembled
Above : Actuators together one incomplete and extended
Hydraulics Online Ltd have completed the upgrade so we decide to test the actuators out of the aircraft.
We test the actuators and find they work well in a no load situation, this is great news.
We revisit Duxford and fit the actuators back to the aircraft, this takes one complete day but we find time to test them.
We still have the same fault. We go home feeling down
The next visit we are determined to complete a nose move
The big day, 12/08/14.
We test for voltage on all the solenoid valves and find we have no voltage to one of the 12.5 degree jacks. We know that we had voltage prior to the actuators being removed so this fault is new.
We complete various tests and find a break in the wiring close to the actuators, this was probably caused by the removal of the actuators however John repairs the wires to airline standard.


Above : John Dunlevy repairs the wiring
Above : John Dunlevy repairs the wiring
We do a test with Ian and Tony looking carefully at the movement of the nose.

We find the nose moves down and up perfectly. The project is a success! The nose is moving perfectly the entire team is so pleased at the success of this project, we have brought the UK its first moving nose since retirement in 2003.
YouTube links to first ever nose move taken on this day -
Above : Ian and Tony look for trouble

Above : John Dunlevy takes in the view

Above : Team for the day, John, Tony, Graham, David (DAS) and Ian
We will revisit to do some remedial work and tidying up. DAS ask us not to divulge that the project has been a success to anyone because they want to announce the project to the media
On the 26th August we revisit again and tidy up the system, we remove ALL the pipes added in the 1980's and re instate the pipe work to the standby selector valve.
We test the system and it works perfectly so we test it again. This time we lower the nose and take some photo's. We are lucky because our founder Steve De Sausmarez has come along, he has not visited or met us since before the project started so it is great to show him how we are doing.

Above : Most of the Heritage Concorde team (for this project)
We revisit again on the 16th September, this is to meet with Brooklands we spend the day allowing the Brooklands team access to the aircraft for photo's and we return the loaned actuator to them. We are pleased to meet the team and we lower the nose to test it and take more photo's.

Above : Heritage Concorde and Brooklands
John Dunlevy is kept busy fitting the intake computers that we have located carefully stored in one of the workshops at Duxford


Above : Intake Racks before
Above : Intake Racks After
On the 20/09/14 we revisit again to train the DAS volunteers on how to complete nose moves at the museum, the day goes well and we come up with a safe working practice that works. The whole of the day is spend doing nose moves.
John Dunlevy reinstates the emergency evacuation lights.
Youtube link -

Above : Abandon aircraft lights

Above : Abandon aircraft light
It is fitting that G-AXDN be the first Concorde to lower its nose in the UK since 2003, G-AXDN is possibly the most important development aircraft for Concorde. She was responsible for testing the new digital computer for the intakes, she had the first full glass visor and was the fastest. After 38 years of being dormant a small part of this aircraft has been brought back to life.

Above : G-AXDN at 17.5 degrees

Above : G-AXDN at 17.5 degrees
Duxford Aviation Society plans a launch for the press, it is planned for the anniversary of retirement of Concorde from commercial service (24th October 2014)
Most of the Heritage Concorde team attend, the event is a complete success and we are pleased with how the whole project has gone.


Above : G-AXDN at 17.5 degrees
Above : G-AXDN and the Red White and Blue colours of the British and French Flags


Above : Capt John Hutchinson enjoys a photo
Above : Invited guests and press

Above : G-AXDN at 12.5 degrees
The Heritage Concorde team would like to thank the following people for making this project a success.
Duxford Aviation Society, without their full support we simply would never have been able to achieve this, they have allowed our engineers to work on an aircraft which is irreplaceable. They have supported and helped our team 100%. They have a collection of 12 very important aircraft, some would argue the most important collection in the UK. Many thanks to DAS and the British Airliner Collection for having the courage to complete this project.
Hydraulics Online Ltd. From the day our team met them they have been supportive and professional and have donated a hydraulic power pack to see this project to its successful end. I have personally visited them at home and when we needed a small upgrade to the power pack they were both keen and helpful to us. Well done Helen and Mark and we look forward to working with you in the near future.
Brooklands restoration team, or more specifically Gordon Roxburgh, they have supported our team and shared information with us. We have a great relationship with Brooklands and we have had an opportunity to meet the team and we will be returning some of the favours by helping and supporting them in the coming months with G-BBDG.
Broughton Lubricants, A big thank you to them, or more specifically Nigel for helping with the oil.