Explore the world of Concorde with Heritage Concorde
All aircraft have the ability to manoeuvre three dimensionally in flight; these manoeuvres are termed pitching, roll and yawing. This section will deal with the use of the control surfaces which Concorde uses to achieve these manoeuvres while in flight.
The delta wing design of Concorde results in the utilization of the control surfaces known as the elevons, for both pitch and roll axes. Dual and independent conventional flight controls (i.e. control column and rudder pedals on the flight deck) are installed at the Captains and First Officer’s stations.
Each wing has six elevons coupled in pairs and each pair of elevons is operated by one twin-body electro-hydraulic power flight control unit (PFCU). The twelve elevens control roll and pitch.
The rudder comprises of two independent sections each operated by one PFCU. The failure of one elevon or one rudder section has no major effect on the flight which can continue with the remaining control surfaces.
Concorde Roll, Pitch and Yaw

There is an emergency flight control system which enables the aircraft to be controlled normally especially during take-off and landing, if the mechanical controls should jam upstream of the relay jacks.

The operation

The pilot’s commands are electrically transmitted to the power flight control units (PFCU). In the event of any electrical failure, the commands are transmitted mechanically by three relay jacks. Each of the three axes (roll, pitch and yaw) is controlled by two electrical channels (Blue and Green) and by a mechanical mode.
In normal operation, the Blue electrical channel is in control, automatically changing over to the Green channel in the event of any failure, with automatic change-over to the mechanical mode if the Green channel should also fail.
There is a flight control surface position indicator (ICOVOL), which is located on the dash panel. This shows the pilot the positions of the control surfaces and which mode (Blue, Green or mechanical.) is in use. The driving of the mechanical mode by the relay jacks cancels all piloting loads inherent in the linkages. While the aircraft is being flown on auto-pilot, the relay jacks also transmit the auto-pilot signals to the PFCU’S.
Hydraulic power is provided to the control systems by a main group comprising the Green and Blue hydraulic systems. There is a standby group consisting of the Yellow system. In the event of any failure of the four aircraft engines, an emergency system pressurizes the Green and Yellow Systems.
Each relay jack comprises a body unit moving on two pistons in tandem. In normal flight operation the aft body unit is supplied by the Blue hydraulic system and the front body unit by the Green hydraulic system
Any pressure drop in a system is signalled to the pilot by warnings. The pilot then replaces the faulty system with the Yellow system using a servo-controls selector switch. The selector switches also allow a main system to be isolated.
The Yaw Control of Concorde


A yaw motion is a side to side movement of the nose of the aircraft as shown in the animation below (This animation does not show a Concorde, but the same principle applies to Concorde which has two rudders for yaw control). The yawing motion is being caused by the deflection of the rudder of this aircraft. The rudder is the hinged section at the rear of the vertical stabilizer which is also known as the fin, Concorde’s fin and two rudders can be seen in the picture to the left.
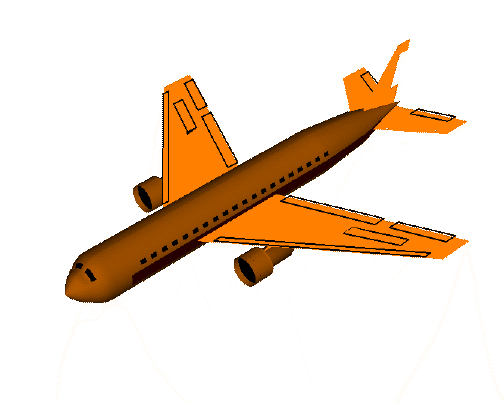
Manual Control
The rudder pedals transmit their movement by bell crank levers and rods through the artificial feel to:
(1) The electrical resolvers of the rudder power flight control units (PFCUS).
(2) The control lever of the relay jack, which drives the PFCU mechanical controls.
The trim wheel, mounted on the centre console, operates the PFCU control resolvers and the relay jack without altering the artificial feel.
The rudder deflections are obtained by electrical control, with the resolvers.
Automatic Pilot
The aircraft is fitted with two automatic pilot systems (Auto Pilot 1 & Auto Pilot 2). These two systems are independent and electrically control the relay jack which, by an auto pilot force limiter drives:
-
The PFCU electrical control resolvers and Captain’s controls
-
The PFCU mechanical control linkage.

The operation
Electrical Control of PFCU’s


After leaving the resolvers, the control of the PFCUS is divided into two channels. The Blue channel and the Green channel, but the Blue channel takes priority. Each PFCU comprises a body which is mechanically linked to the rudders and is moved by two jacks in tandem attached to the aircraft structure. Each half of the PFCU body contains an electrically controlled spool-valve which is associated with a servo-valve and an electro-valve.
The hydraulic pressure in each half of the body is controlled by the spool-valve and the electro-valve. By analogy with the hydraulic system which supplies them, the components of each body-half are termed Blue if they use the BLUE system and Green if they use the GREEN system. If nothing abnormal is disclosed by the electrical monitoring system, the Blue electro-valve opens and pressure is admitted to the Blue electro-valve, the Green electro-valve remains closed.
Electrical signals, transmitted by the Blue channel, control the proportional opening of the servo-valve. The signal regulated servo-valves receives the hydraulic pressure admitted by the electro-valve.
The regulated pressure displaces the blue spool-valve which, because of the mechanical linkage, moves the green spool-valve. The blue and green hydraulic pressures at the spool-valves are directed to the annular section of the jacks and the
PFCU body then moves in the same direction as the spool-valves. The movement stops when the PFCU finds a position of rest relative to the new position of the spool-valves thus blocking the hydraulic pressure inlet ports.
The Monitoring System
The Blue and Green electro-valves are controlled by an electronic monitoring system.
When in normal control, when this system detects a fault during the flight phase, it automatically closes the Blue electro-valve and opens the Green electro-valve. The Green electro-valve is then controlled by the Green electrical channel and activates the Green spool-valve. If the monitoring system detects a new fault, it closes the Green electro-valve. At that point an internal hydraulic system in the PFCU then locks the spool-valves mechanical control lever.
Mechanical control
The relay jack, which is mechanically controlled by the flight controls, operates the PFCU spool valves by means of cables rods and relays.

Each relay jack comprises of a body which is attached to the PFCU spool-valve control linkage. The body is moved by two jacks in tandem which are attached to the aircraft structure.
Each half of the body contains an electrically controlled spool-valve which is associated with a servo-valve and an electro-valve. Hydraulic pressure in each half of the body is held back by the spool-valve and the electro-valve and locks the relay jack control lever on the spool-valve.
This lever, mechanically operated by the flight controls, moves the spool-valves.
The Blue and Green hydraulic pressures are then directed to the annular sections of the jacks and the relay jack body moves in the same direction as the spool-valves.
The movement stops when the body finds a position of rest relative to the position of the spool-valves thus blocking the hydraulic pressure inlet ports.

The Automatic Pilot
By analogy with the hydraulic pressure which supplies them, the components of each body half are called Blue if they use the BLUE system and Green if they use the Green system.
AP1 electrically controls the relay jack via the Blue servo-valve, AP2 via the Green servo-valve.
If nothing abnormal is disclosed by the AP electronic monitoring system, the Blue electro-valve opens; Blue hydraulic pressure is admitted to the Blue servo-valve and operates on the servo-valve mechanical control lever locking system.
This hydraulic locking jack unlocks the control lever from the spool-valves and locks it on to the relay jack body.
The AP1 control signal opens the blue servo-valve proportionally which regulates the hydraulic pressure admitted to the electro-valve.
This regulated pressure moves the Blue spool valve which, being mechanically attached to the Green spool valves, is also moved.
The Blue and Green hydraulic pressures held back by the spool-valves are now directed to the annular sections of the jacks, the relay jack body moves in the same direction as the spool-valves thus blocking the pressure inlet ports.
The relay jack displacement moves the input lever, which is locked on to its body, together with the PFCU mechanical control linkage.
The input lever displacement controls the PFCU electrical resolvers and the manual flight controls via the Auto Pilot force limiter.
In the AP1 mode, the relay jack monitoring system is supplied and opens the blue electro-valve.
When the system detects a fault during flight phase, it automatically closes the blue electro-valve and trips AP1.
The input Lever is again locked on to the spool-valves thus re- establishing manual control. If the pilot wishes to continue his flight in Auto Pilot (AP), he must switch on AP2, which functions in the same way as API but using the Green hydraulic system.
The Roll Control of Concorde


When Concorde’s elevons are deflected differentially they provide the roll control for Concorde, which then causes the aircraft to behave in a similar way to that of a traditional aircraft’s ailerons, which are seen in the animation below, which illustrates roll control.
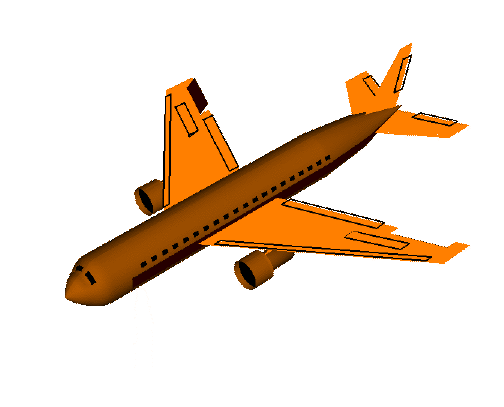
The animation above is not of Concorde, but details a roll axis, which lies along the aircraft centreline. A roll motion is an up and down movement of the wings of the aircraft as shown in this animation.

Manual Control
The controls transmit their movement by cables, levers and rods through the artificial feel (AF) to the following:
(1) The electrical resolvers of the elevon PFCU’s.
(2) The control lever of the relay jack which drives the PFCU mechanical controls.
There is a trim wheel, which is mounted on the centre console in the flight deck compartment, and operates the PFCU control resolvers and the relay jack without altering the artificial feel.
The relative elevon deflections are obtained by electrical control, via the resolvers and by mechanised control via a mechanical, system called a mixing unit.
Automatic pilot
Concorde is fitted with two automatic pilot systems (AP1 and AP2). These two systems are independent and electrically control the relay jack which, by an auto pilot force limiter drives the PFCU electrical control resolvers, the PFCU mechanical control linkage and the Captain’s controls.
The operation of Roll Control on Concorde

Electrical Control of PFCU’s
After leaving the resolvers, the control of the PFCUs is divided into two channels. The Blue channel and the Green channel, the Blue channel takes priority.
Each PFCU, comprises of a body which is mechanically linked to the elevons and is moved by two jacks in tandem which are attached to the aircraft structure.
Each half of the PFCU body contains an electrically controlled spool-valve which is associated with a servo-valve and an electro-valve.
The hydraulic pressure in each half of the body is controlled by the spool-valve and the electro-valve.
By analogy with the hydraulic system the components of each body-half are which supplies them, termed Blue if they use the BLUE system and Green if they use the GREEN system.
If nothing abnormal is disclosed by the electrical monitoring system, the Blue electro-valve opens and pressure is admitted to the Blue servo-valve. The Green electro-valve remains closed.
Electrical signals which are transmitted by the Blue channel control the proportional opening of the servo-valve.
The signal regulated servo-valve receives the hydraulic pressure admitted by the electro-valve.
The regulated pressure displaces the Blue spool-valve which because of the mechanical linkage moves the Green spool-valve.
The Blue and Green hydraulic pressures at the spool valves are directed to the annular section of the jacks and the PFCU body then moves in the same direction as the spool valves. The movement stops when the PFCU finds a position of rest relative to the new position of the spool-valves thus blocking the hydraulic pressure inlet ports.
The Monitoring System
The Blue and Green electro-valves are controlled by an electronic monitoring system.
During normal control, when this system detects a fault during the flight phase, it automatically closes the Blue electro-valve and opens the Green electro-valve.
The Green servo-valve is then controlled by the Green electrical channel and activates the Green spool-valve.
If the monitoring system detects a new fault, it closes the Green electro-valve and an internal hydraulic system in the PFCU then locks the spool-valves mechanical control lever.
Mechanical Control

The relay jack, mechanically controlled by the flight controls, operates the PFCU spool-valves by means of cables, rods and relays.
Each relay jack comprises of a body attached to the PFCU spool-valve control linkages.
The body is moved by two jacks in tandem which are attached to the aircraft structure.
Each half of the body contains an electrically controlled spool valve which is associated with a servo-valve and an electro-valve.
Hydraulic power in each half of the body is held back by the spool-valve and the electro-valve, and locks the relay jack control lever on the spool-valves.
This lever, which is mechanically operated by the flight controls, moves the spool-valves. The Blue and Green hydraulic pressures are then directed to the annular sections of the jacks and the relay Jack body moves in the same direction as the spool-valves. The movement stops when the body finds a position of rest relative to the position of the spool-valves thus blocking the hydraulic pressure input ports.
Auto Pilot
By analogy with the hydraulic pressure which supplies them, the components of each body half are called Blue if they use the BLUE system and Green if they use the GREEN system.
Auto Pilot 1 electrically controls the relay jack via the Blue servo-valve, Auto Pilot 2 via the Green servo-valve. If nothing abnormal is disclosed by the Auto Pilot electronic monitoring system, the Blue electro-valve opens; Blue hydraulic pressure is admitted to the Blue servo-valve and operates on the servo-valve mechanical control lever locking system.
This hydraulic locking jack unlocks the control lever from the spool-valves and locks it on to the relay jack body.
The Auto Pilot 1 control signal opens the Blue servo-valve proportionally which regulates the hydraulic pressure admitted to the electro-valve. This regulated pressure moves the Blue spool-valve which, being mechanically attached to the Green spool-valve, is also moved.
The Blue and Green hydraulic pressures which are held back by the spool-valves are now directed to the annular sections of the jacks, the relay jack body moves in the same direction as the spool valves thus blocking the pressure input ports.
The relay jack displacement moves the input lever, which is locked on to its body, together with the PFCU mechanical control linkage.
The input lever displacement controls the PFCU electrical control resolvers and the manual flight controls via the Auto Pilot force limiter.
In the Auto Pilot 1 mode, the relay jack monitoring system is supplied and opens the Blue electro-valve. When the system detects a Fault during flight phase it automatically closes the Blue electro-valve and trips Auto Pilot 1.
The input lever is again locked on to the spool-valves thus re-establishing manual control. If the pilot wishes to continue his flight in Auto Pilot, he must switch on Auto Pilot 2, which functions in the same way as Auto Pilot 1, but using the Green hydraulic system.
The Pitch Control of Concorde
Pitch is the upwards and downwards movement of Concorde nose, this type of movement can be seen in the animation of another type of aircraft below.


When Concorde’s elevons move together in the upwards direction as seen in the picture below, they cause Concorde to pitch up, similarly when they move together in the downwards direction Concorde will pitch down.

Manual Control
The control columns transmit their movement by cranks and rods and through the artificial feel system (AF) to the following:
-
The powered flight control units (PFCU) electrical control channel resolvers,
-
The control lever of the relay jacks which drives the PFCU mechanical controls.
There are trim control wheels located on the centre pedestal between the Captain and First Office which operate:
-
The PFCU resolvers,
-
The relay jack, without affecting the artificial feel.
The relative eleven defections are obtained by:
-
Electrical controls via the resolvers,
-
Mechanical control via a mechanical system known as the mixing unit.
Auto Pilot
The aircraft is equipped with two auto pilot systems (APs). These two systems (AP1 and AP2), are independent and electrically control the relay jacks which drives in turn, via an auto pilot force limiter the following:
-
The PFCU electrical control channel resolvers,
-
The relay jack mechanical control linkage.
The Operation of Pitch Control
PFCU Electrical Control
After leaving the resolvers, the control of the PFCU’s is divided into two channels, the Blue channel and the Green channel, the Blue channel takes priority.
Each PFCU comprises of a body which is mechanically linked to the elevens and is moved by two jacks in tandem and attached to the aircraft structure. Each half of the PFCU body contains an electrically controlled spool-valve which is associated with a servo-valve and an electro-valve.
The hydraulic pressure in each half of the body is controlled by the spool-valve and the electro-valve. By analogy with the hydraulic system which supplies them, the components of each body-half are termed Blue if they use the Blue system and Green if they use the Green system.
If nothing abnormal is disclosed by the electrical monitoring system, the Blue electro-valve opens and pressure is admitted to the Blue servo-valve. The Green electro-valve remains closed.
Electrical signals transmitted by the Blue channel control the proportional opening of the servo-valve. The signal regulated servo-valve receives the hydraulic pressure admitted by the electro-valve. The regulated pressure displaces the Blue spool-valve which being mechanically linked to the Green spool-valve moves the latter.
The Blue and Green hydraulic pressures at the spool-valves are directed to the annular section of the jacks and the PFCU body then moves in the same direction as the spool-valves. The movement stops when the PFCU body finds a position of rest relative to the new position of the spool valves thus blocking the hydraulic pressure inlet ports.
Monitoring Channel
The Blue and Green electro-valves are controlled by an electronic monitoring system.
During normal control conditions, when this system detects a fault during the flight phase, it automatically closes the Blue electro-valve and opens the Green electro-valve. The Green servo-valve is then controlled by the Green electrical channels and activates the Green spool-valve.
If the monitoring system detects a new fault it then closes the Green electro-valve. An internal hydraulic system in the PFCU will then lock the spool-valve mechanical control lever.
Mechanical Control
The relay jack which is mechanically controlled by the flight controls operates the PFCU spool-valves by means of cables rods and bell-cranks. Each relay jack comprises a body attached to the PFCU spool-valve control linkage. The body is moved by two jacks in tandem which are attached to the aircraft structure. Each half of the body contains an electrically controlled spool-valve which is associated with a servo-valve and an electro-valve.
Hydraulic power in each half of the body is held back by the spool-valve and the electro-valve, and locks the relay jack control lever on the spool-valves.
This lever mechanically operated by the flight controls, moves the spool-valves.
The Blue and Green hydraulic pressures are then directed to the annular sections of the jacks and the relay jack body moves in the same direction as the spool-valves.
The movement stops when the body finds a position of rest relative to the new position of the spool-valves, thus blocking the hydraulic pressure inlet ports.
Auto Pilot (AP)
By analogy with the hydraulic pressure which supplies them, the components of each body half are called Blue if they use the Blue system and Green if they use the Green system.
API electrically controls the relay jack by the Blue servo-valve, AP2 by the Green servo-valve.
If nothing abnormal is disclosed by the Auto Pilot electronic monitoring system, the Blue electro-valve opens; Blue hydraulic pressure is admitted to the Blue servo-valve and operates on the servo-valve mechanical control lever locking system.
This hydraulic locking jack unlocks the control lever from the spool-valves and locks it on to the relay jack body. The AP1 control signal opens the Blue servo-valve proportionally which regulates the hydraulic pressure admitted to the electro-valve.
This regulated pressure moves the Blue spool-valve which, being mechanically attached to the Green spool-valve, is also moved.
The Blue and Green hydraulic pressures held back by the spool-valves are now directed to the annular sections of the jacks, the relay jack body moves in the same direction as the spool-valves thus blocking the pressure inlet ports.
The relay jack displacement moves the input lever, which is locked on to its body, together with the PFCU mechanical control linkage. The input lever displacement control’s the PFCU electrical control resolvers and the manual flight controls via the Auto Pilot force Limiter.
In the AP1 mode, the relay jack monitoring system is supplied and opens the Blue electro-valve. When the system detects a fault during flight phase, it automatically closes the Blue electro-valve and trips AP1.
The input lever is again locked on to the spool-valves thus re-establishing manual control. If the pilot wishes to continue his flight in Auto Pilot, he must switch on Auto Pilot 2, which functions in the same way as Auto Pilot 1 but using the Green hydraulic system.